Starlink pan-tilt mount and satellite tracker

A description of this project will be posted soon. In the mean time, you can view the work in progress photos below.
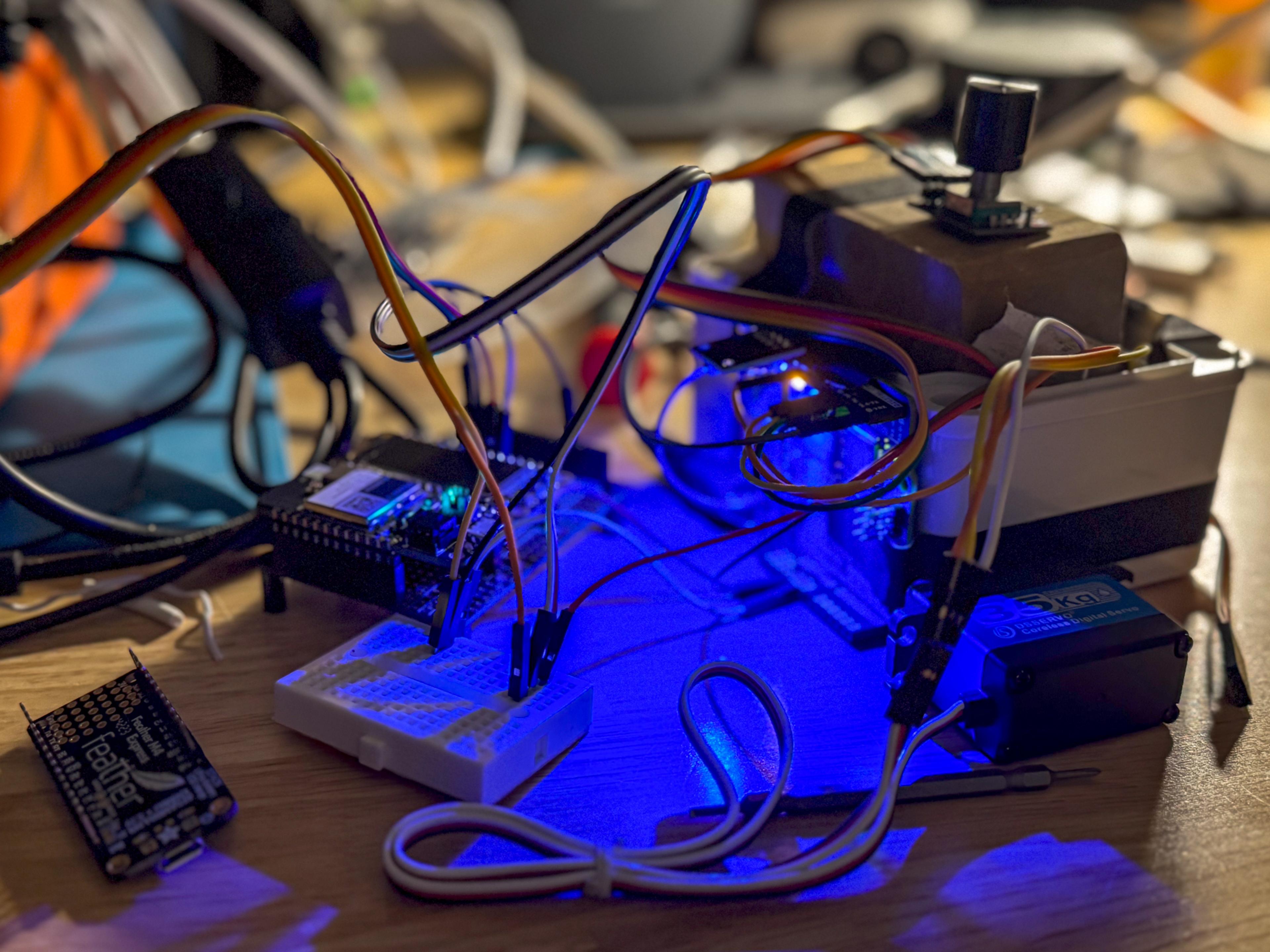
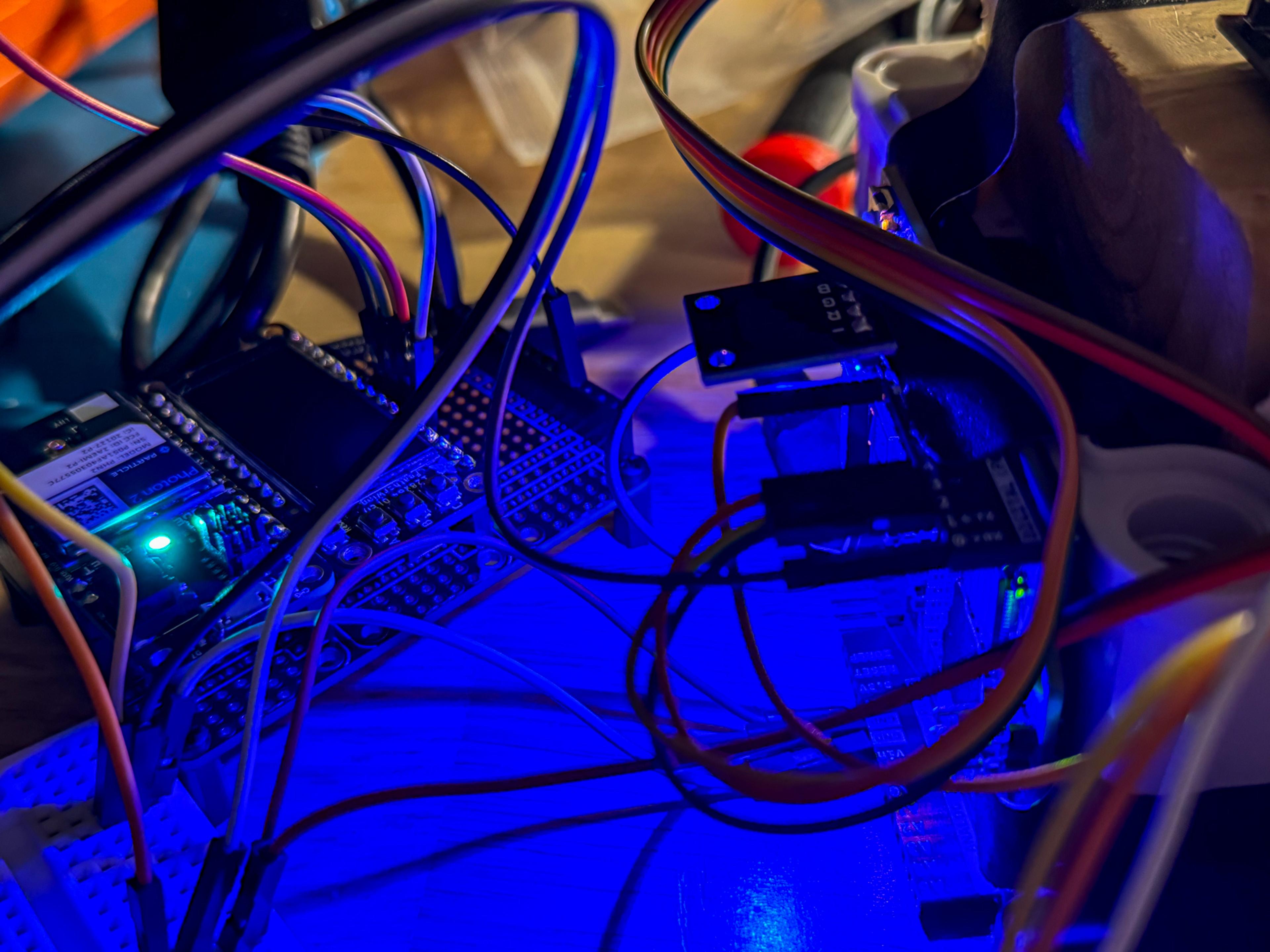
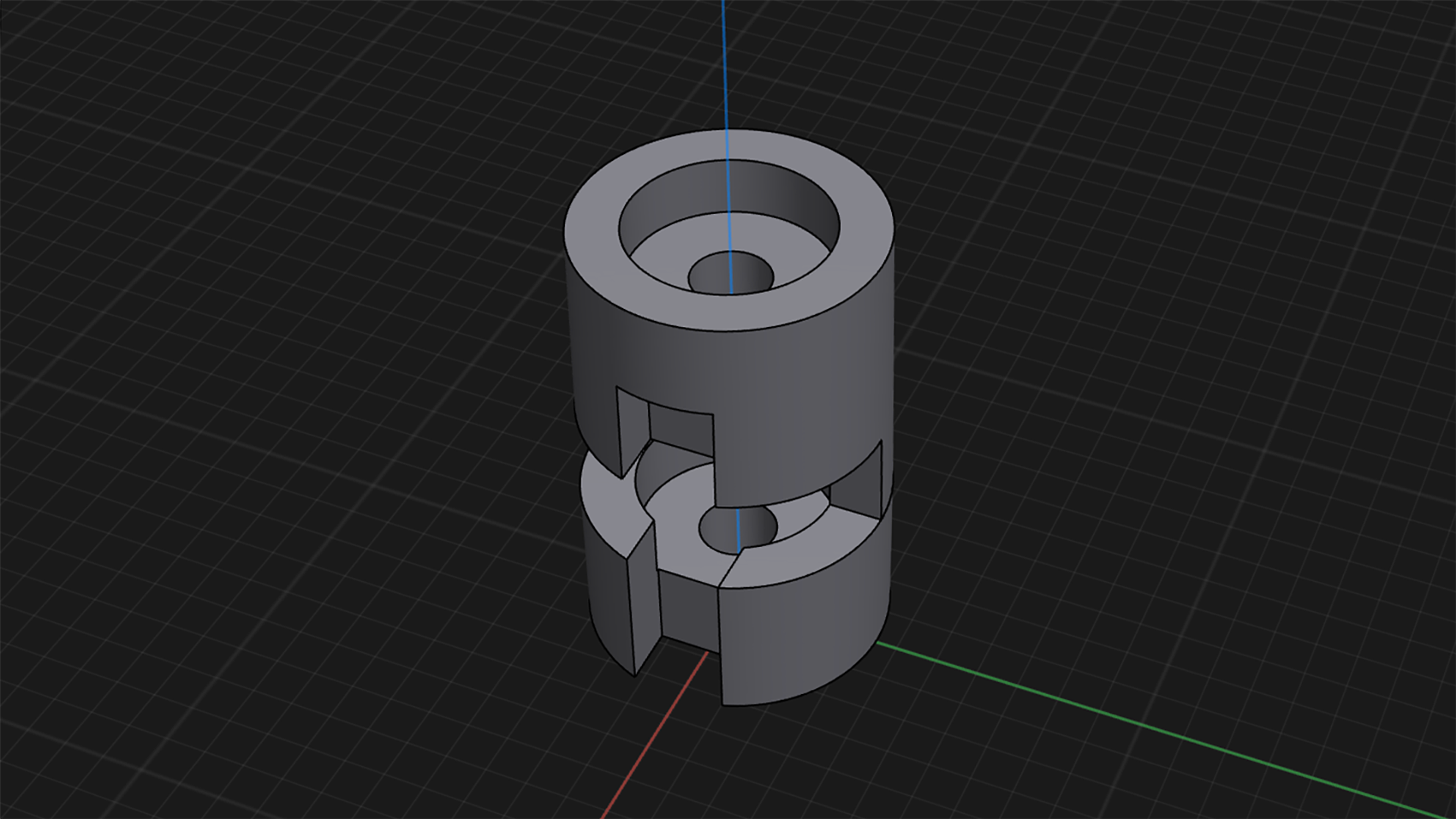
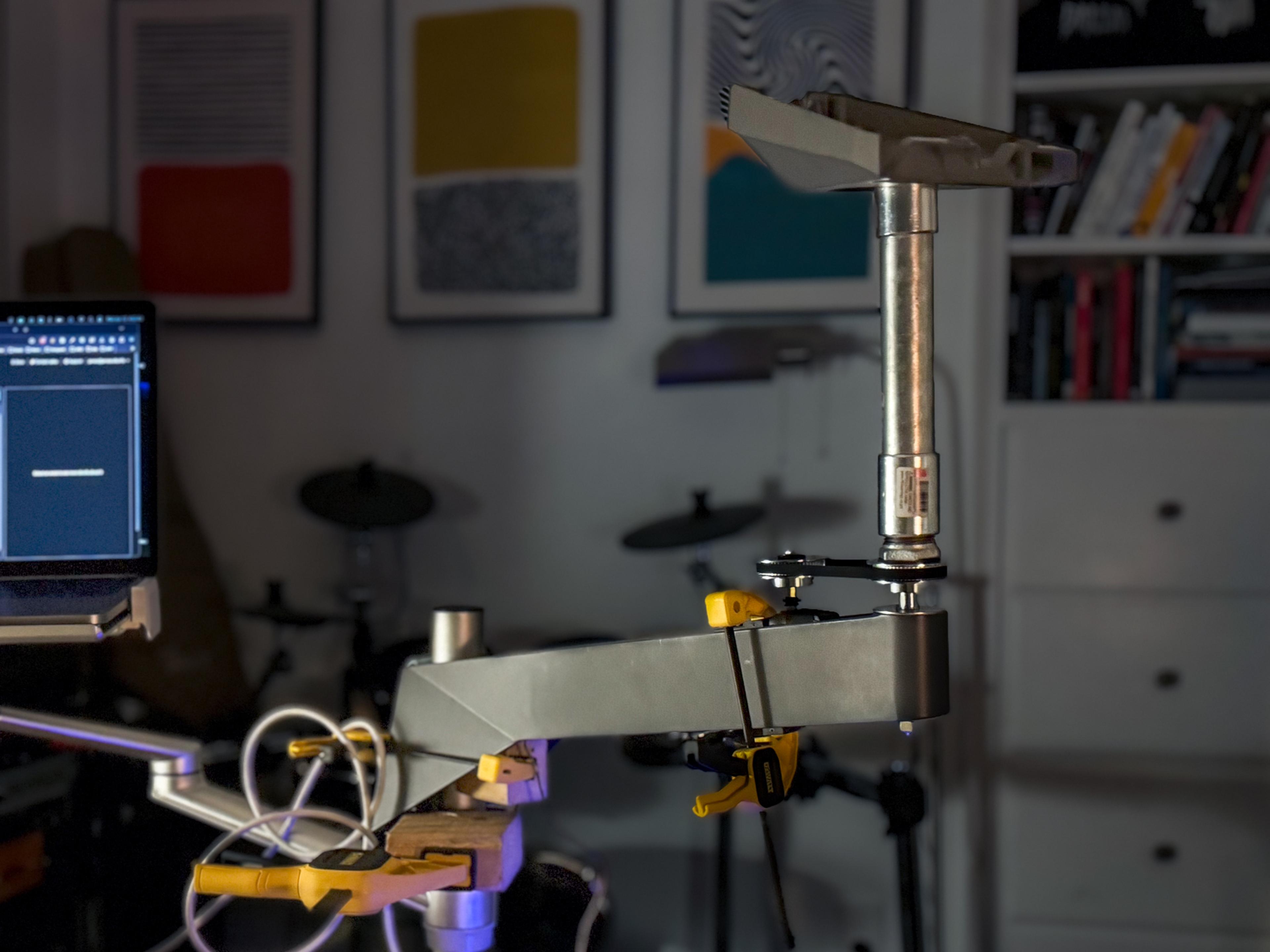
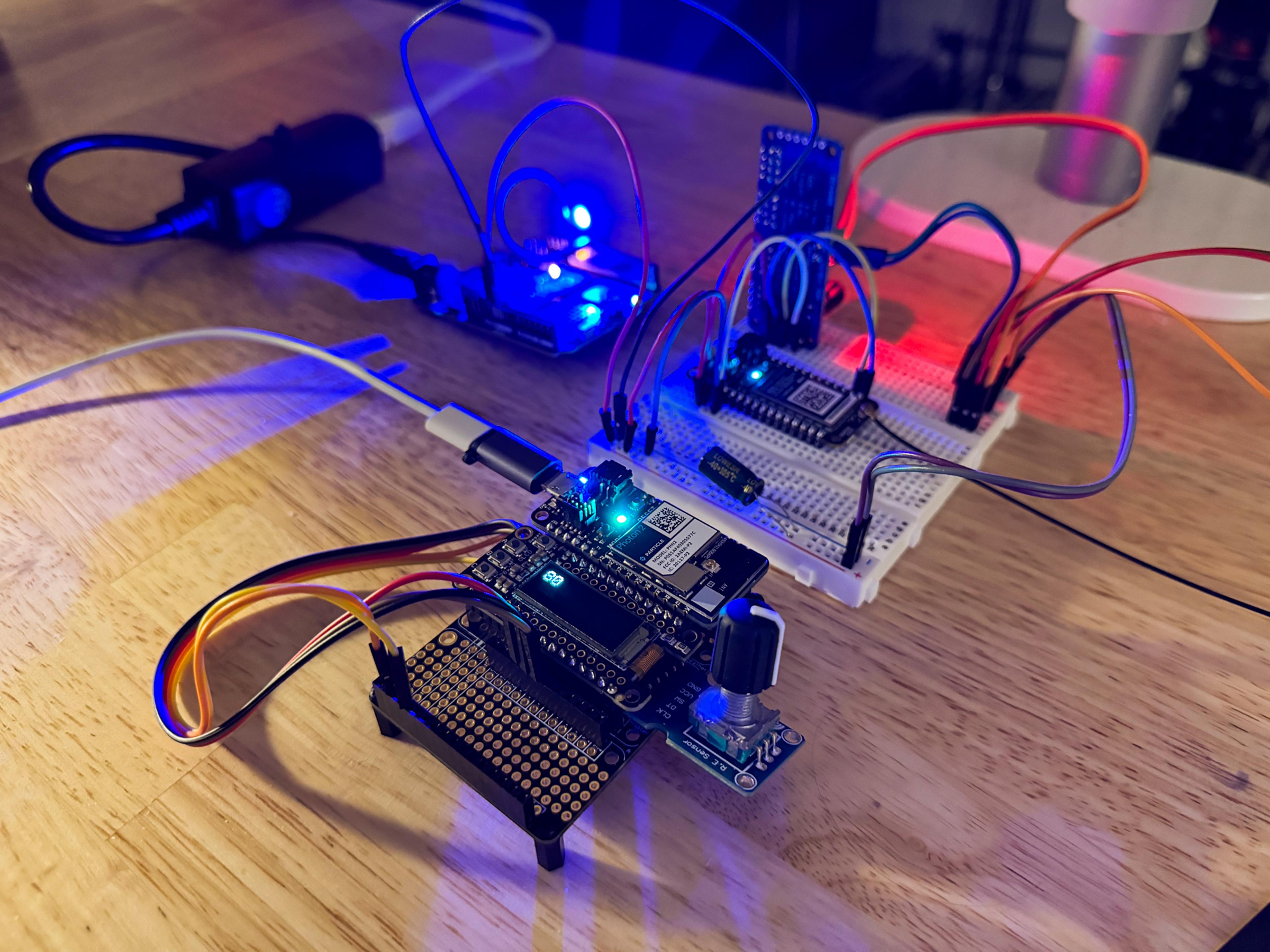
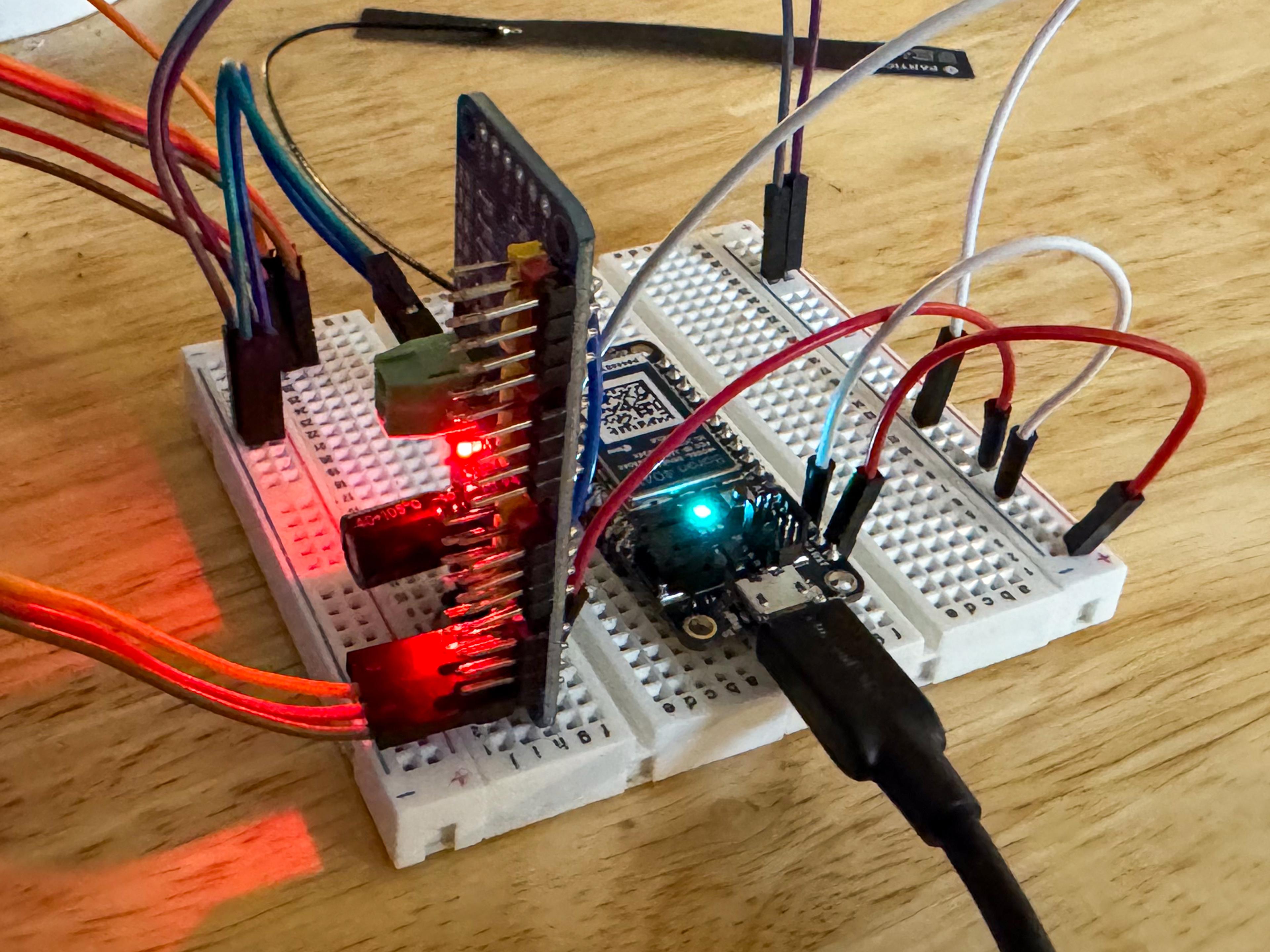
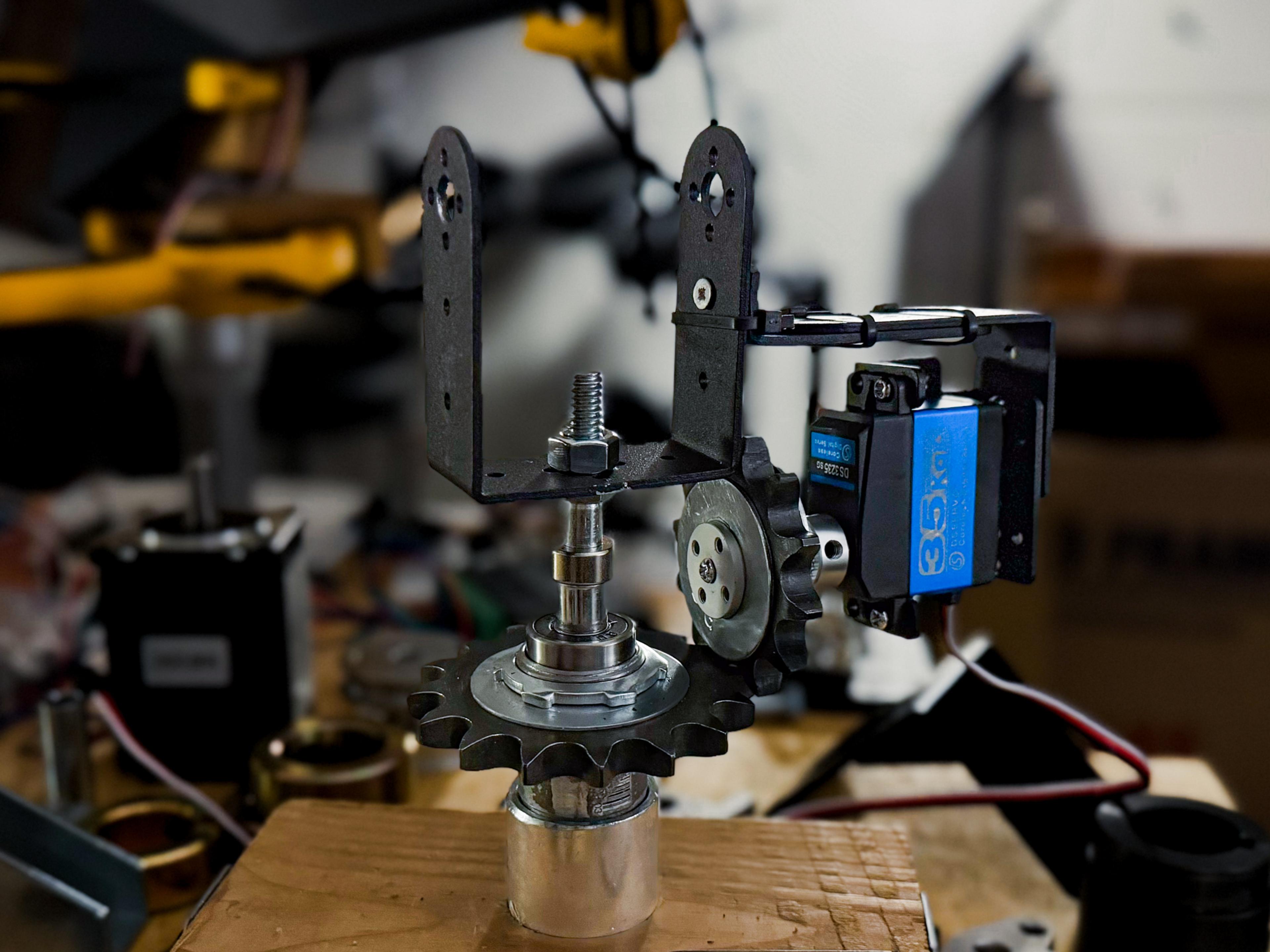
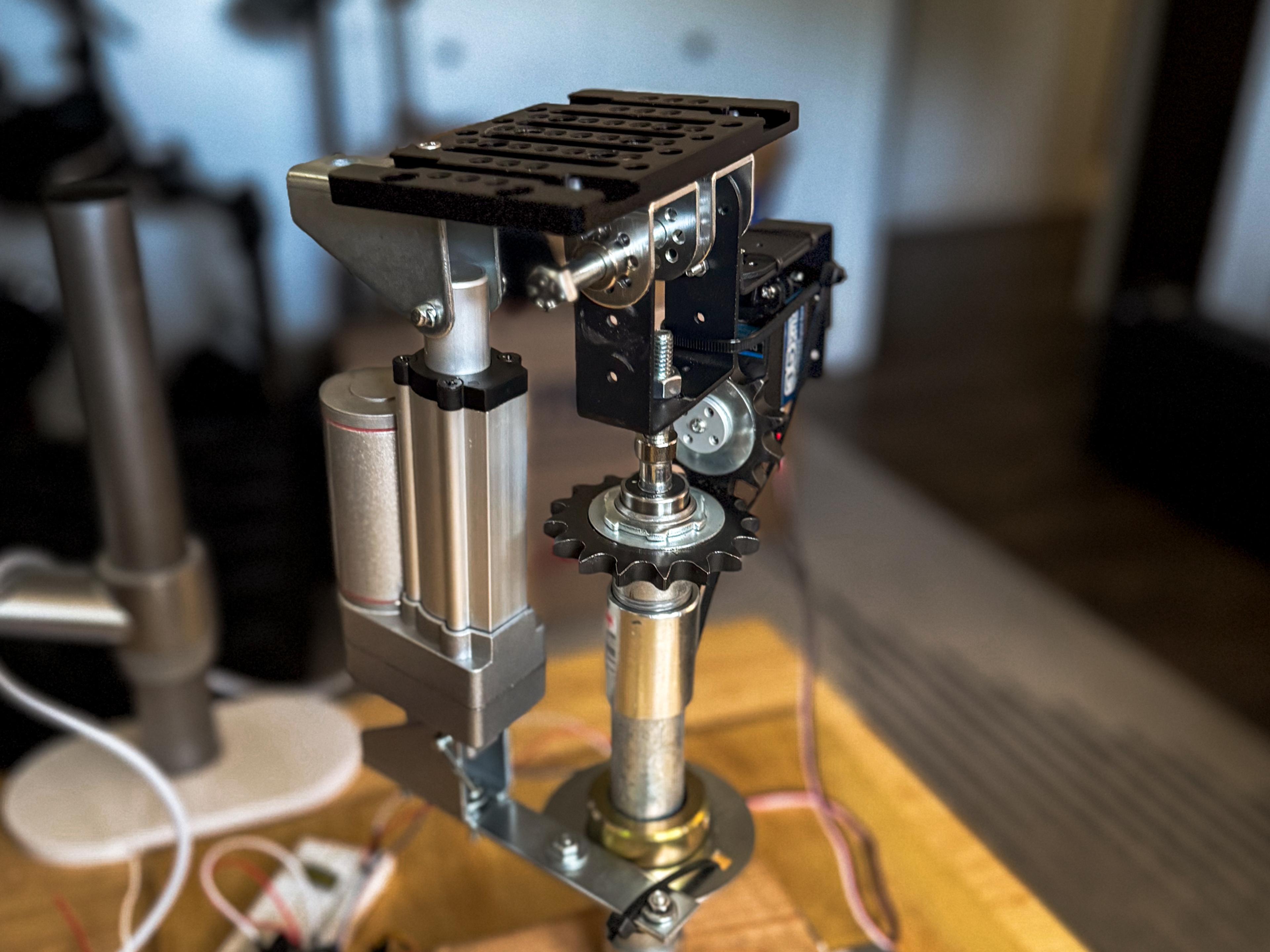
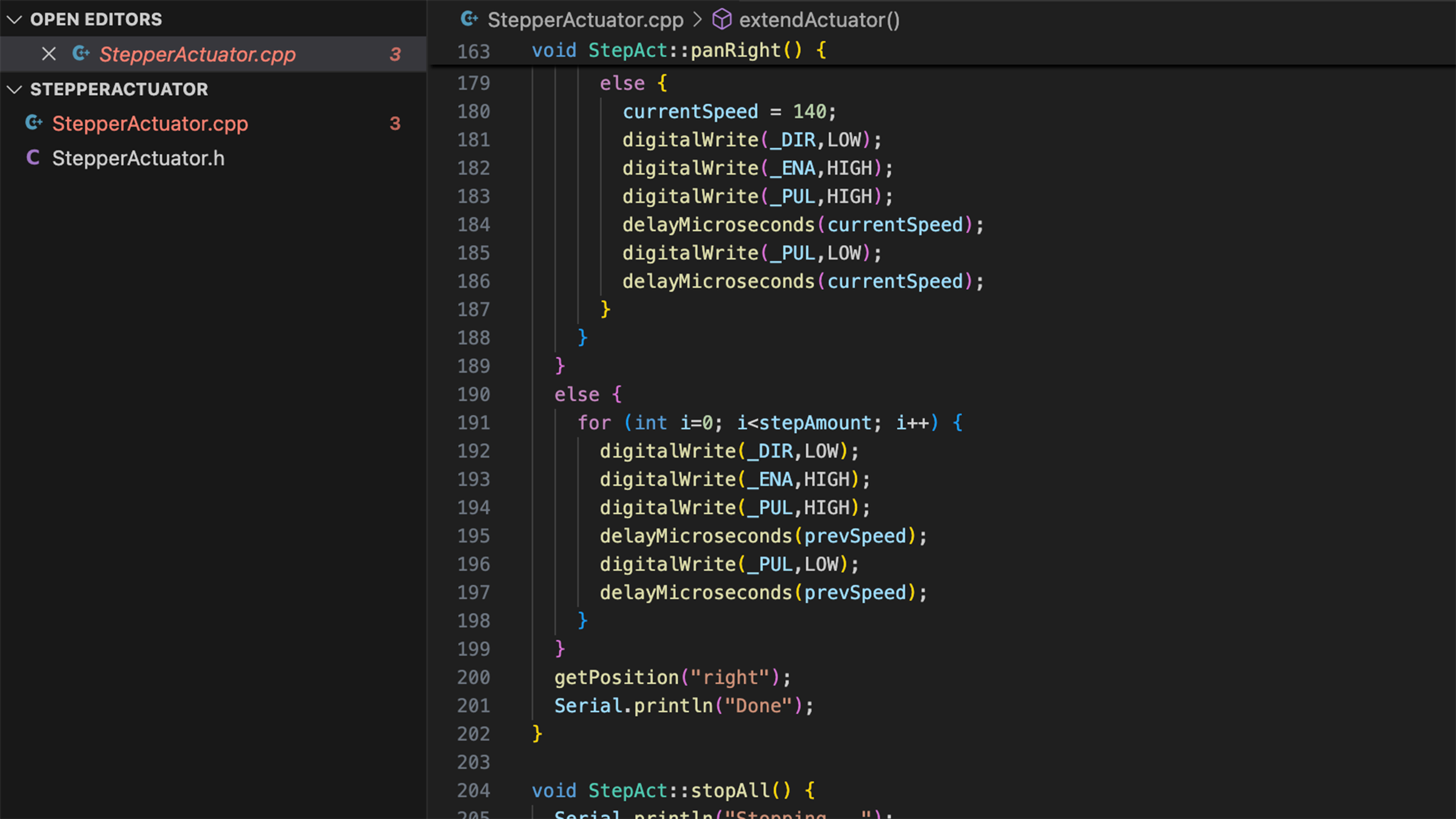
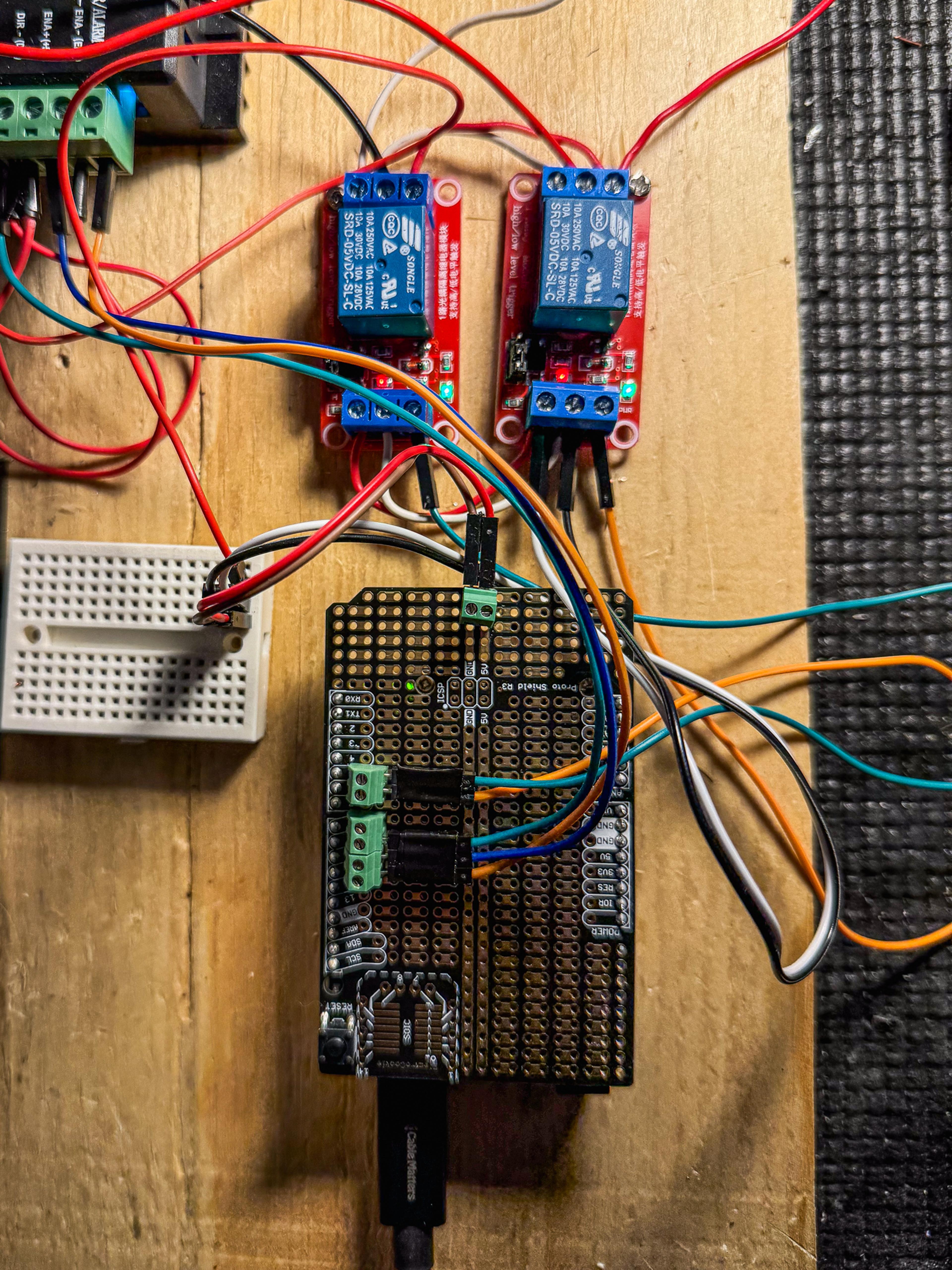
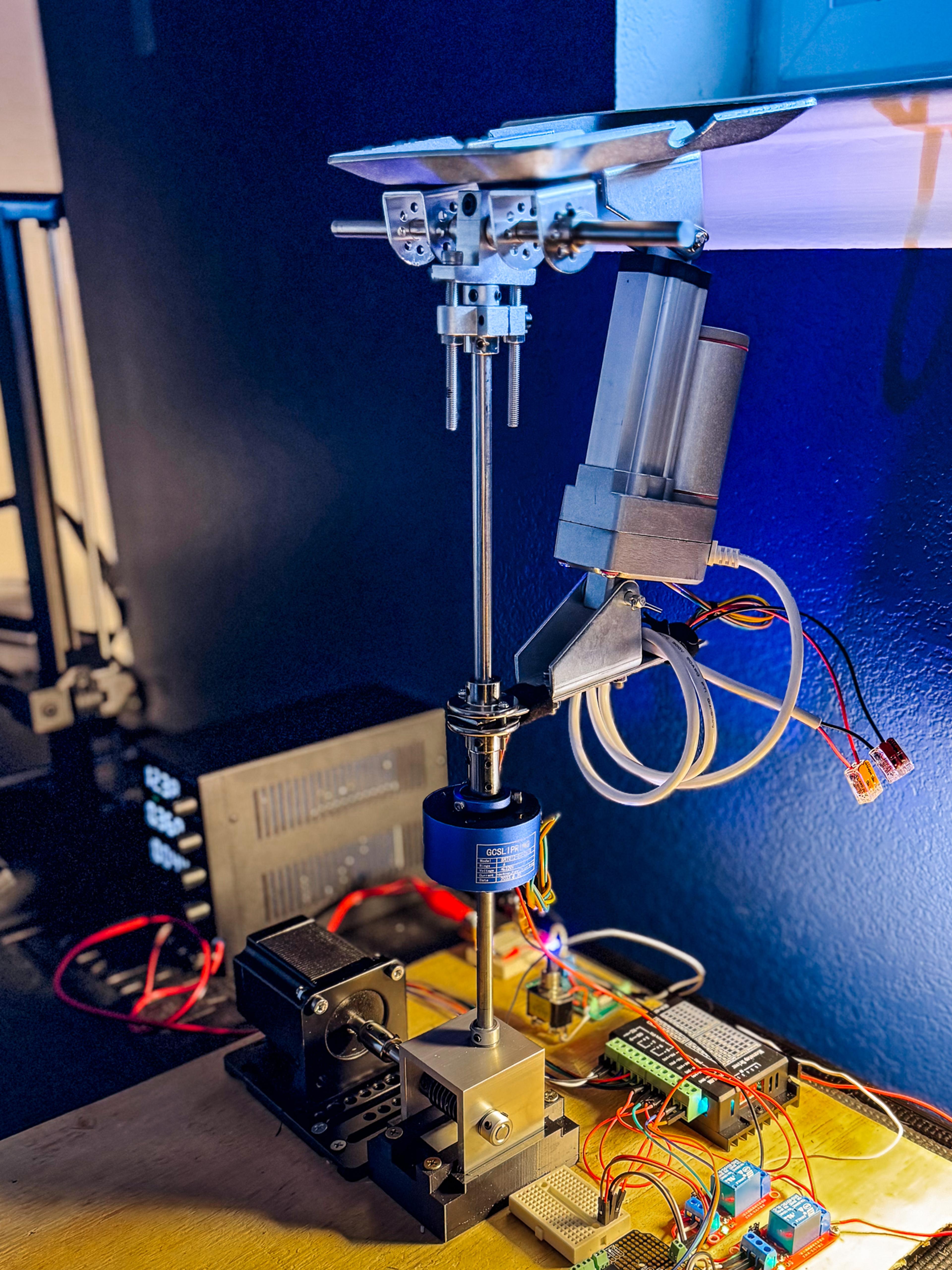
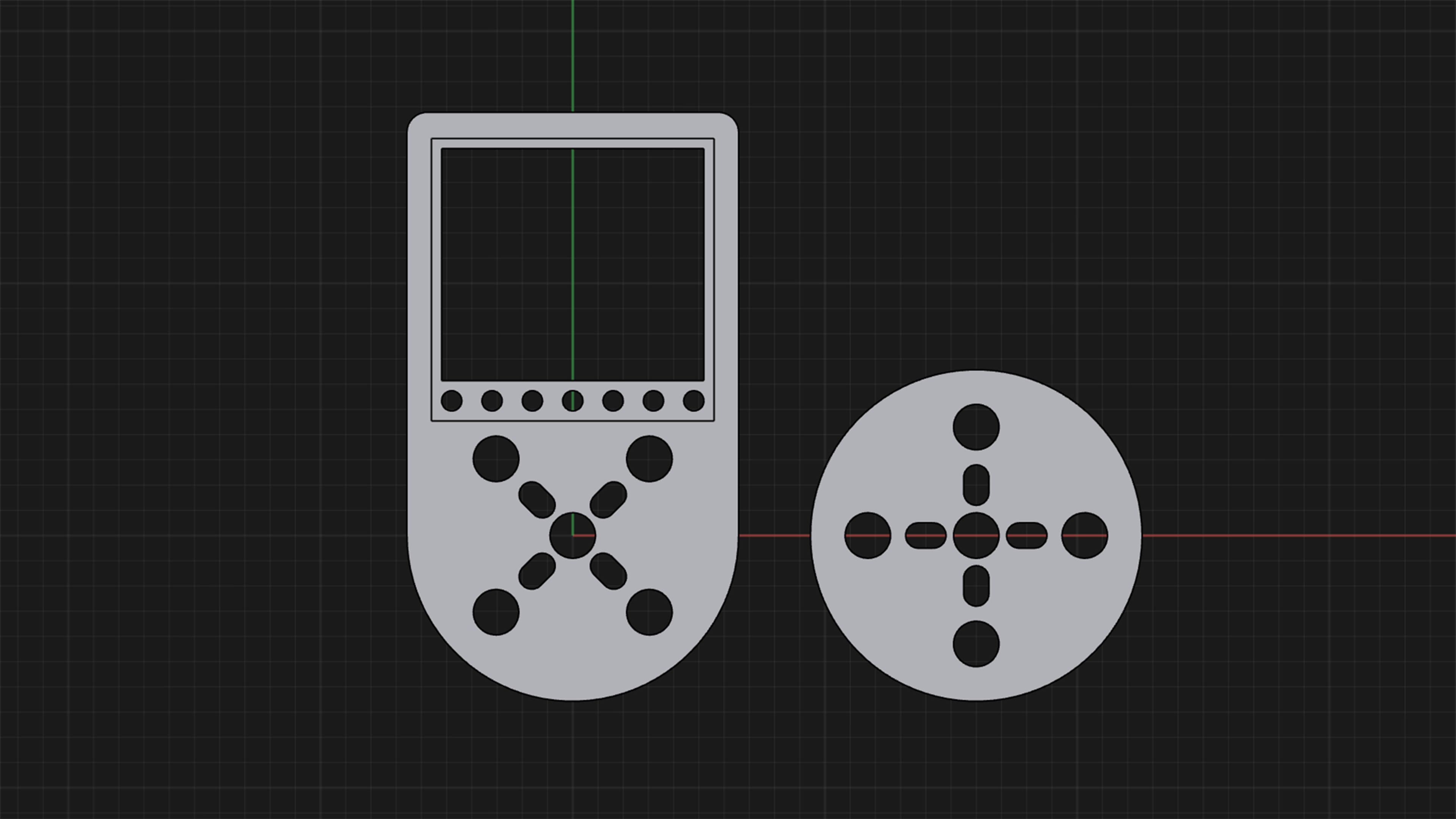
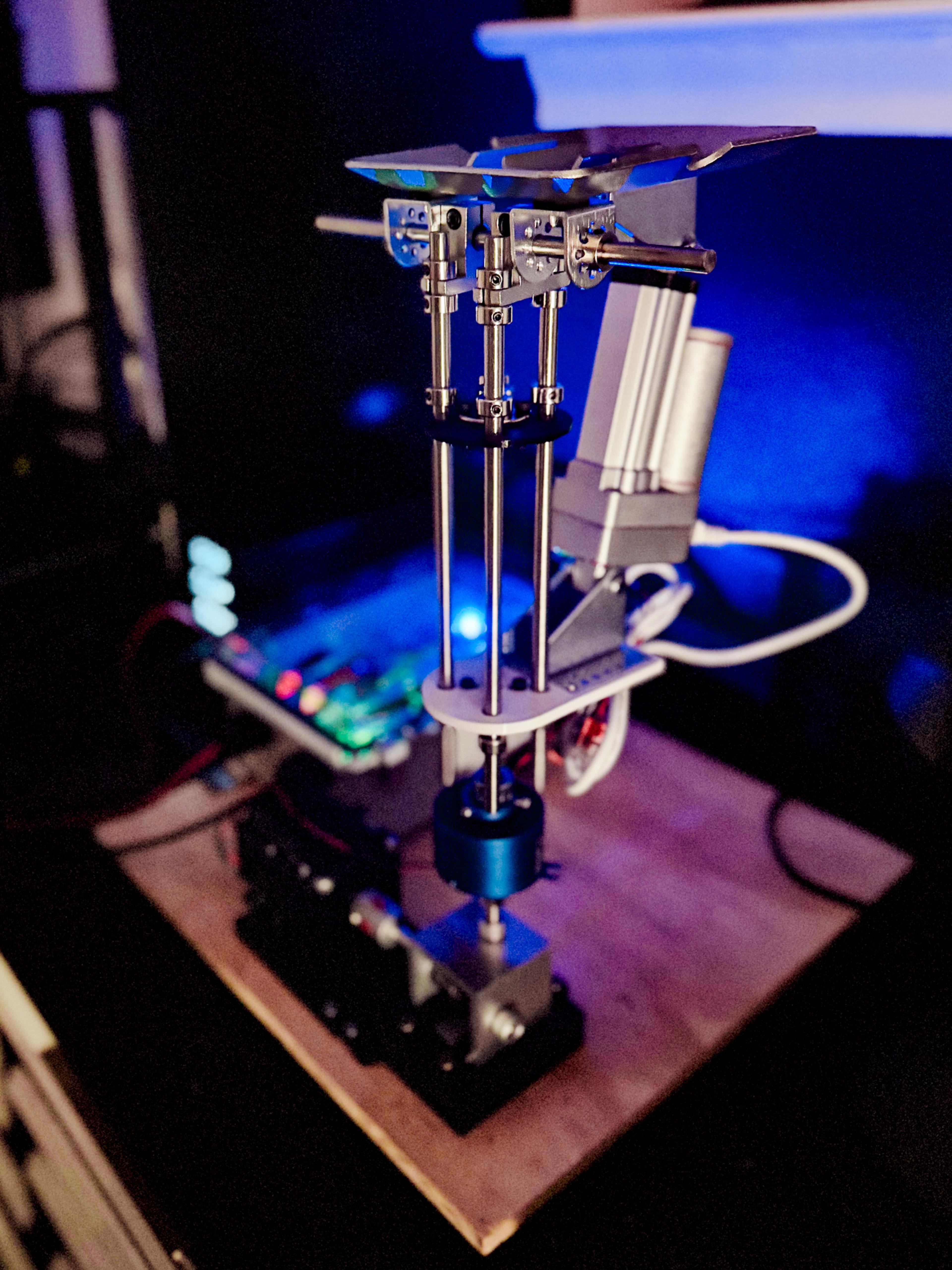
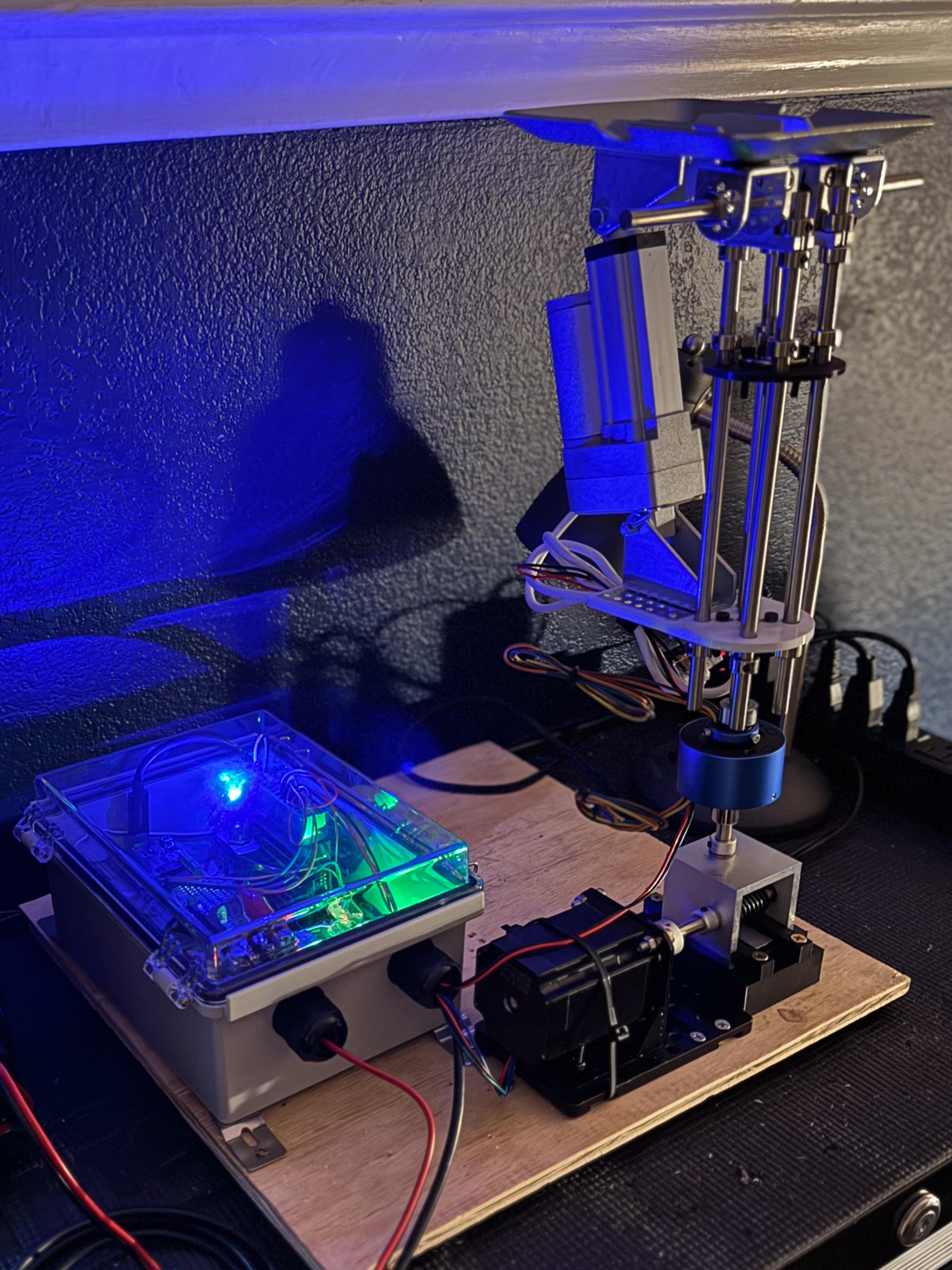
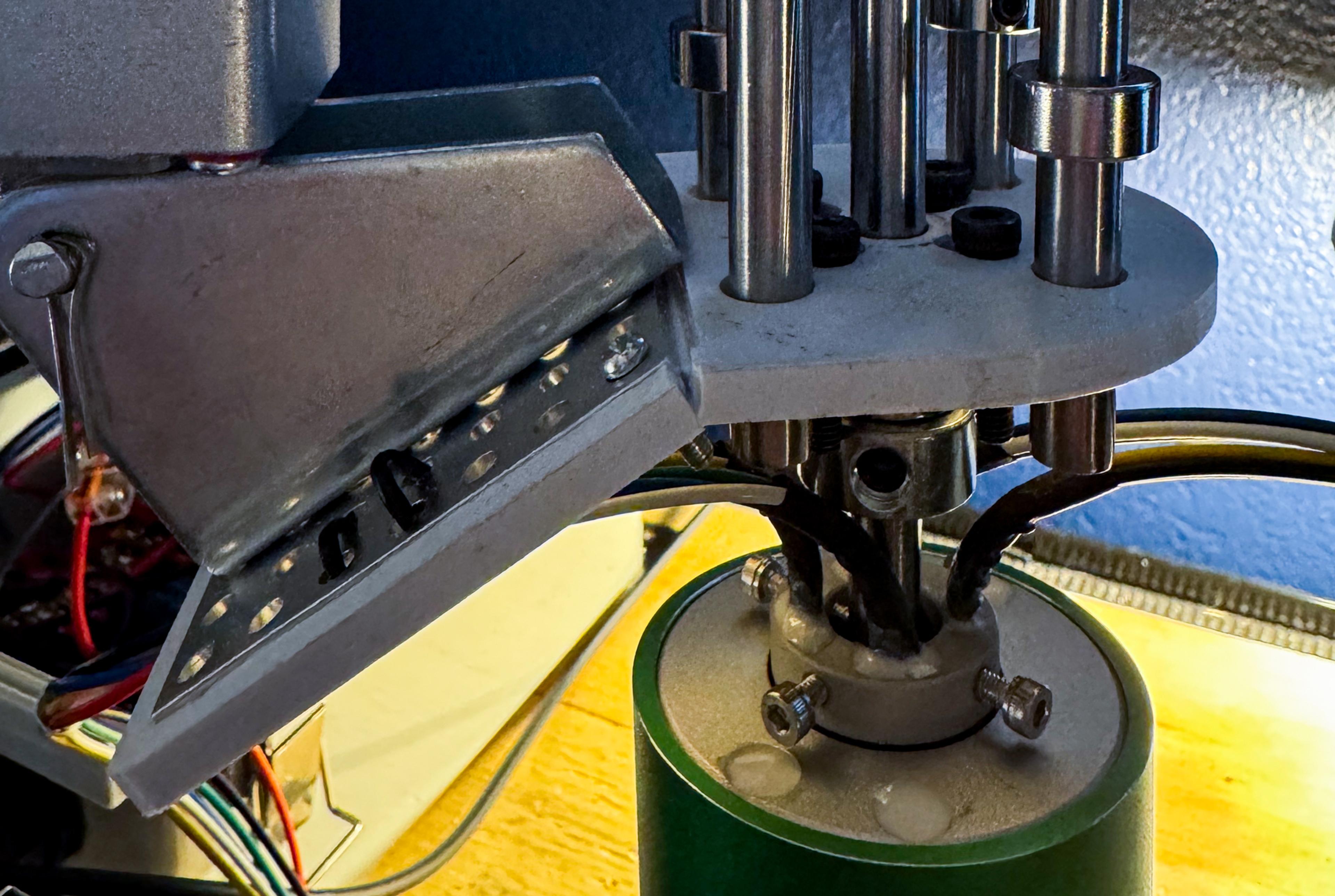
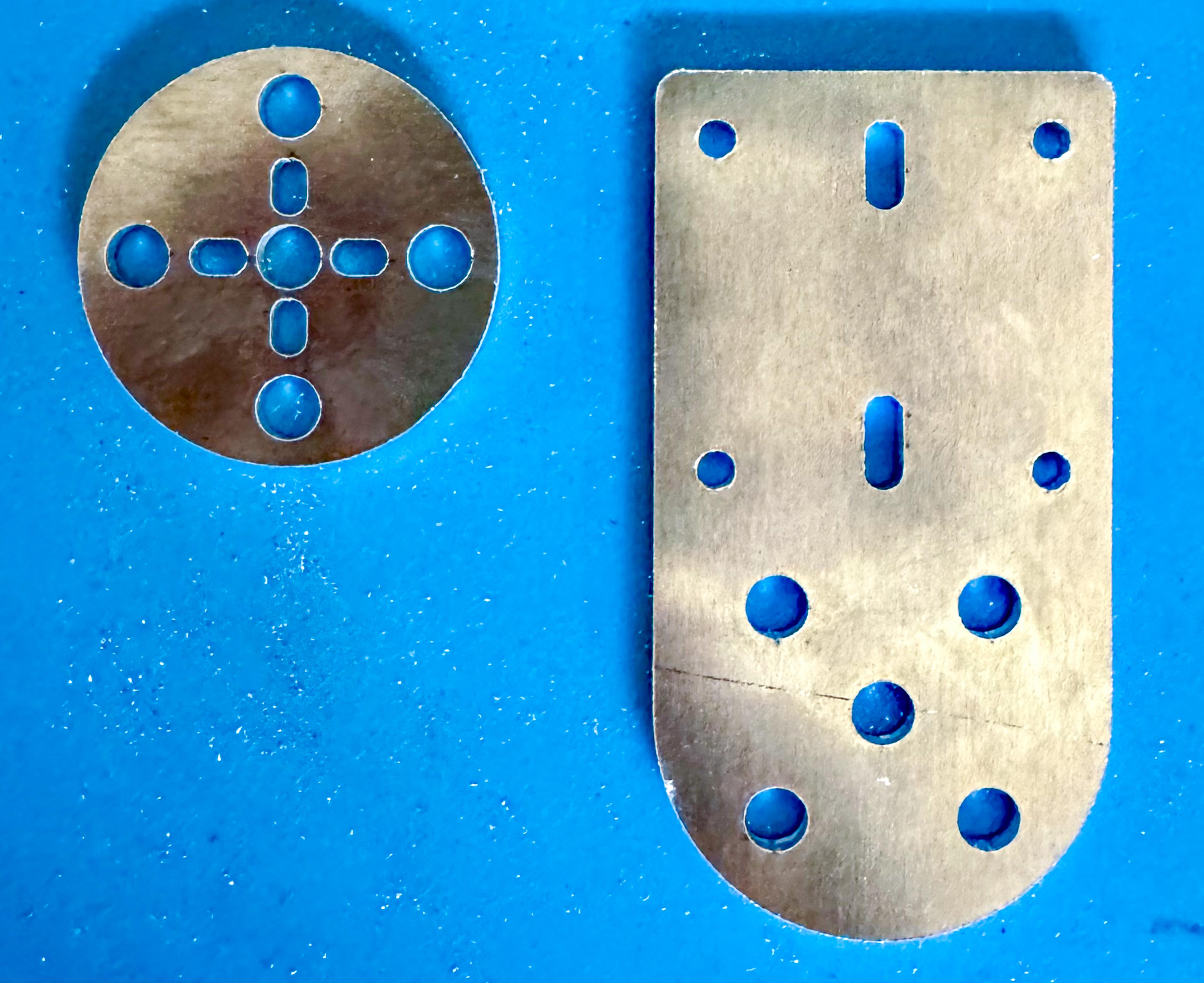
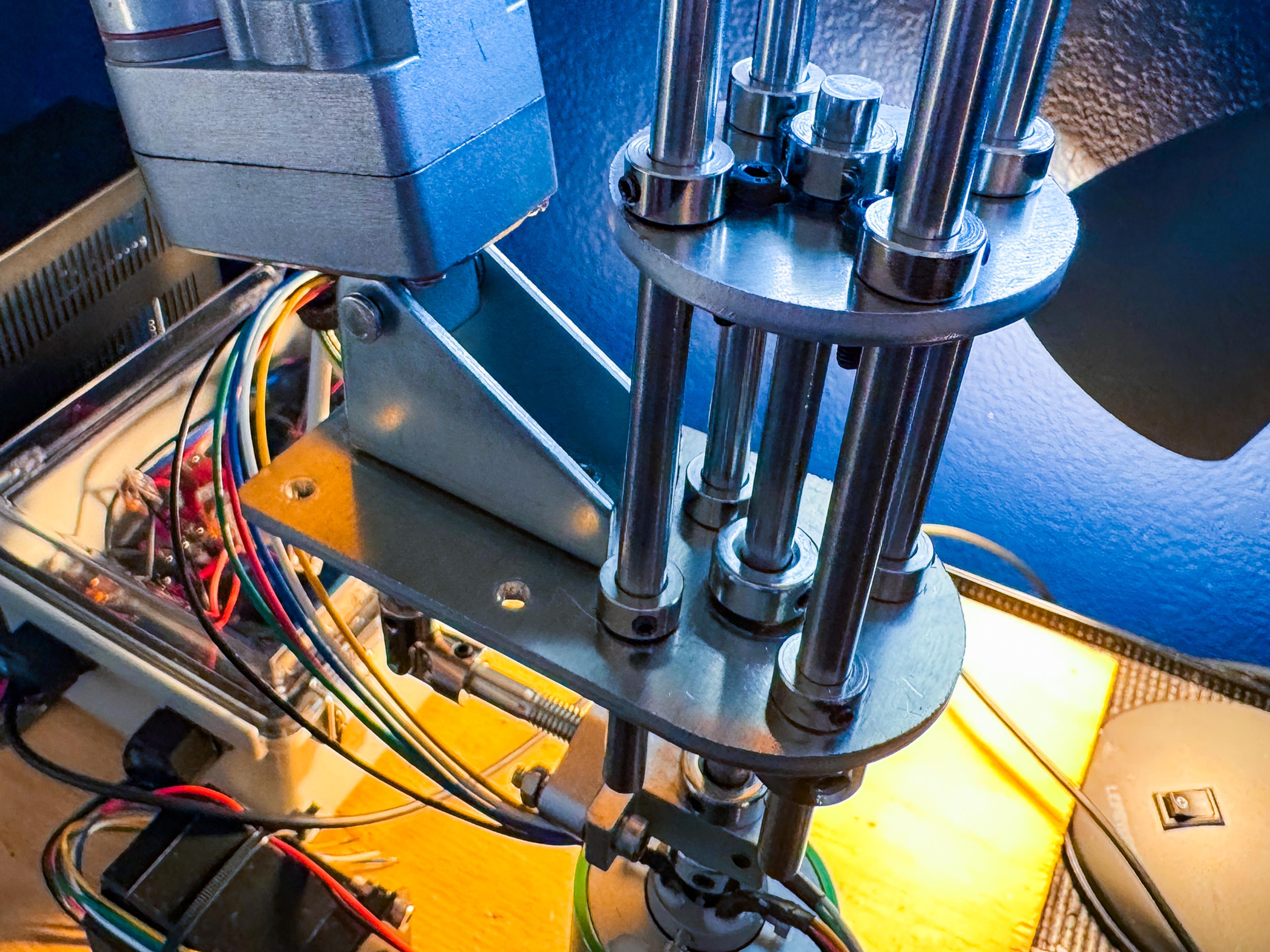
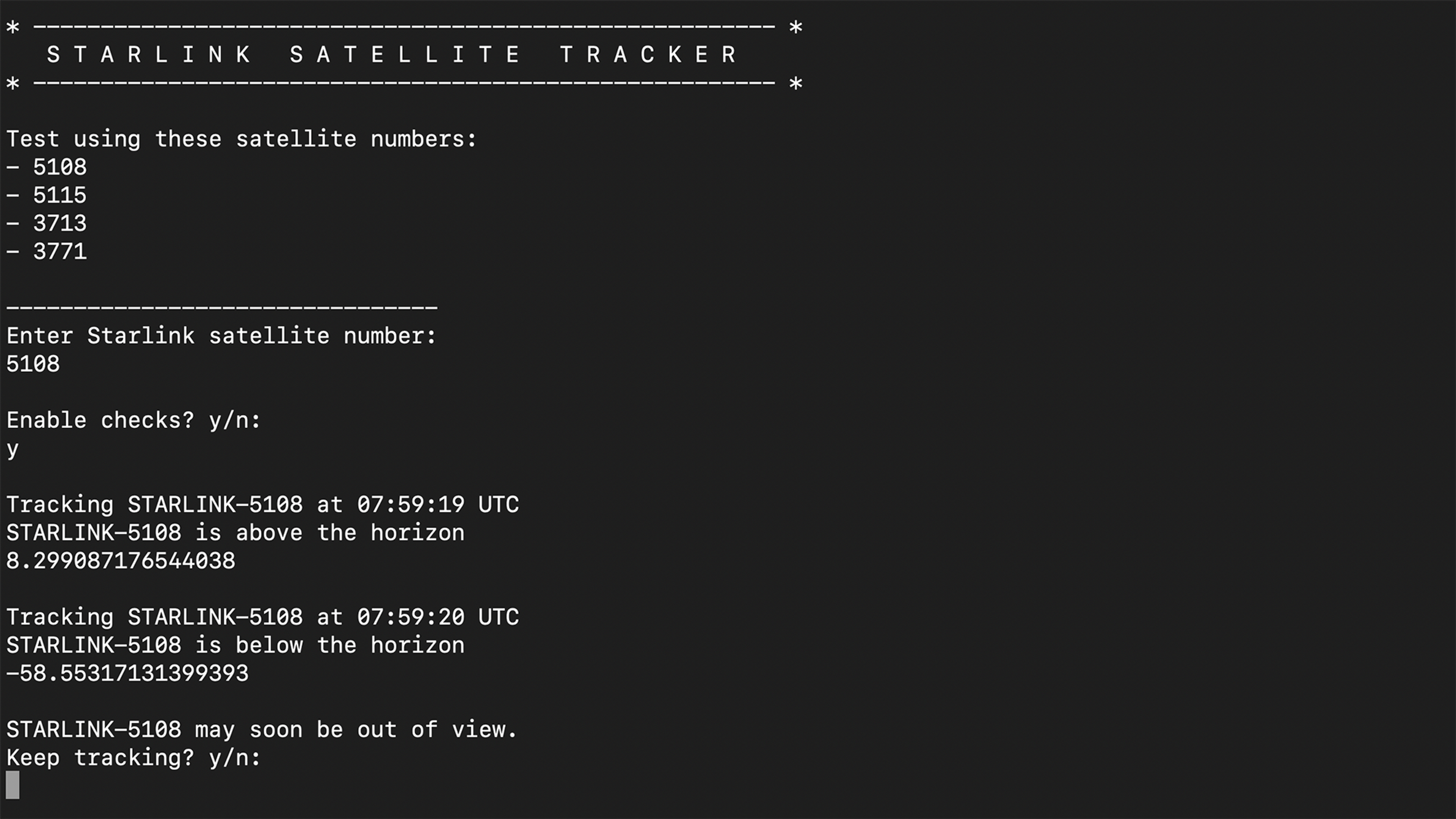
A description of this project will be posted soon. In the mean time, you can view the work in progress photos below.